Root Cause Analysis (RCA) Quick Guide
What is root cause analysis?
In today’s fast-paced laboratory environments, problem-solving is not just about fixing symptoms but addressing the root causes of problems to prevent them from recurring. Root Cause Analysis (RCA) is a critical methodology used to uncover these underlying problems and create long-term solutions. More than just a troubleshooting tool, RCA plays a pivotal role in regulatory compliance, helping labs maintain data integrity, timely documentation, and continuous improvement. Regulatory bodies, such as the FDA and ISO, emphasize the importance of using RCA to demonstrate proactive risk management and continuous improvement. In this context, labs must ensure that RCA processes are well-documented, timely, and integrate supply chain oversight.
The RCA Guide: Your Quick Reference Tool
At LabHQ, we understand how critical RCA is for quality control and compliance in laboratory settings. That’s why we’ve developed a simple yet effective 5-step RCA Quick Guide to help lab professionals streamline their problem-solving process while meeting regulatory demands. This quick guide emphasizes maintaining data integrity and compliance with timelines while facilitating continuous improvement across your operations.
Here’s a breakdown of our 5-step process:
Step 1: Define the Problem
Clarify the issue and its impact.
- Ask: Why is this problem important? What do you hope to achieve by solving it?
- Detail: Name the process that’s being affected and specify the problem in detail.
- Document: Define the problem with complete, accurate data, and verify that all relevant records are up to date and compliant with regulatory standards.
Step 2: Identify Possible Causes
Gather facts and data to determine possible causes.
- Gather: Collect facts and data, like reports, equipment logs, and observations.
- Fact check: Verify your measurement system and data integrity to ensure the information is accurate and tamper-proof.
- Develop: Develop clear statements for the probable causes.
- Document: Data should be complete, traceable, and aligned with compliance requirements.
Step 3: Test Possible Causes
Use data analysis to find the root cause.
- Analyze: Analyze data using practical, graphical, and statistical tools to identify trends and anomalies.
- Design and Test: Test assumptions by designing controlled experiments to determine cause-and-effect relationships
- Verify: Verify the most probable root cause through repeated testing.
- Document: Document all results and findings.
Step 4: Identify Solutions
Develop and evaluate continuous improvement opportunities.
- Innovate: Innovate and define potential improvement opportunities with solutions like equipment adjustments, procedural updates, or staff retraining.
- Perform: Conduct a cost-benefit analysis (such as a return on investment) to select the most efficient solution.
- Assess: Assess if any improvements can be extended to other processes.
- Align: Esure that long-term corrective actions align with continuous improvement goals.
- Document: Document all actions for compliance reporting.
Step 5: Control and Monitor
Implement and document changes.
- Implement: Implement the solution aligned with your quality management system.
- Monitor: Monitor the process post-implementation to make sure the issue does not recur and that benefits are realized.
- Document: Document all changes and improvements in a timely manner, including what happened and any root causes identified.
- Summarize: Summarize key learnings to help improve future problem analysis
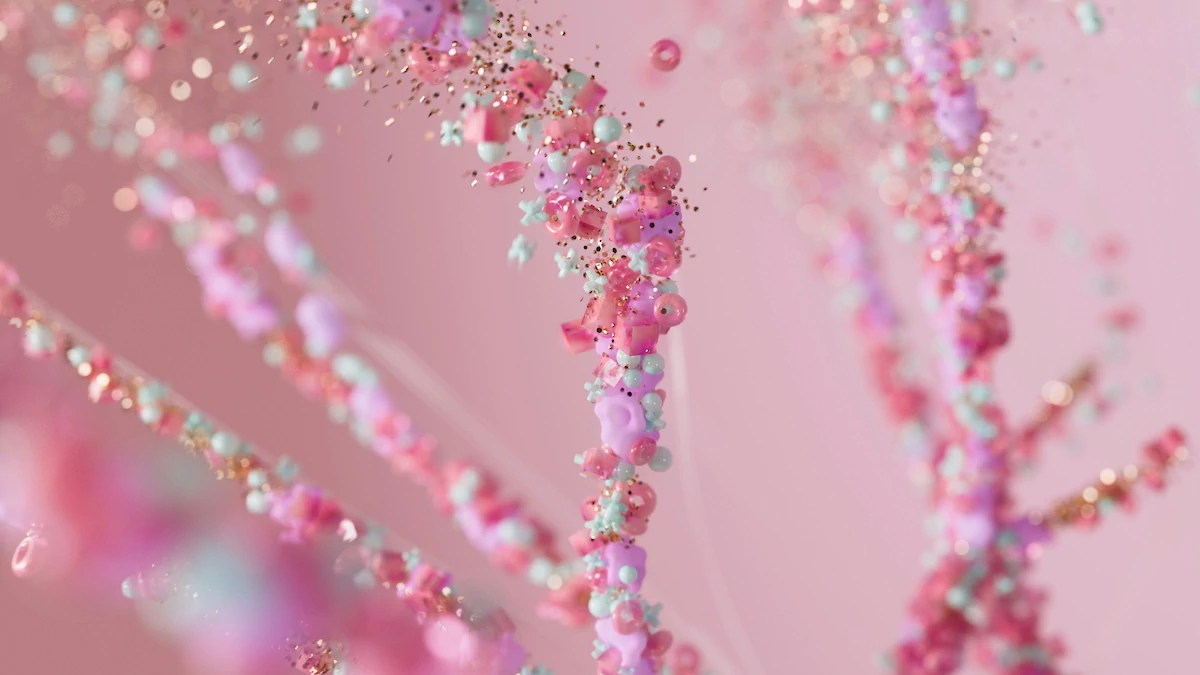