Crude Oil Assay & Quality Control: Critical Tests and the Impact of Automated Processes
In this context, a Laboratory Information Management System (LIMS) offers labs of all sizes a practical approach to streamlining operations. By automating workflows, organizing data, and providing straightforward access to essential information, LIMS helps labs stay compliant, manage quality efficiently, and adapt quickly to changing demands. This article explores how LIMS can support QC and QA managers in tasks like managing sulfur levels in marine fuels or meeting cetane requirements in diesel, ultimately helping labs achieve consistent, reliable outcomes.
Key Tests in Crude Oil Assay & Quality Control
Distillation (ASTM D86, ASTM D1160)
Distillation breaks down crude oil into its components by boiling point, a core process for products like gasoline, diesel, and jet fuel. For instance, refining operations use distillation to achieve the right octane rating in gasoline or the desired cetane number in diesel. Accurate distillation also supports fuel blending at distribution points, ensuring compliance with environmental regulations, like low-sulfur diesel mandates.
Metals Content (ASTM D5708, ASTM D5863, IP 501)
Testing for metals like vanadium, nickel, and iron is crucial for maintaining refining processes and ensuring product quality, especially in jet and marine fuels. In bulk fuel terminals, trace metal testing helps verify the effectiveness of metal deactivators in fuel additives, preventing corrosion and enhancing safety during transport.
Chlorides (ASTM D4929, UOP 779, UOP 588)
Detecting chlorides is essential to prevent corrosion in refining equipment and maintain fuel stability during storage and transport. For aviation fuel distributors, managing chloride levels is crucial to maintain the quality of Jet A-1 fuel, ensuring it meets stringent standards for global aviation safety. This test is also vital for bulk fuel terminals, where preventing chloride contamination ensures the safe storage and handling of products like kerosene and heating oil. Marine fuel producers rely on accurate chloride testing to protect shipboard machinery and ensure fuel stability over long voyages.
Sulfur Content (ASTM D4294, ASTM D2622)
Sulfur control is a big deal in fuel production, especially with evolving regulations for low-sulfur gasoline and diesel. For industrial fuel suppliers and marine fuel producers, accurate sulfur testing ensures compliance and prevents equipment damage due to corrosive residues. Automotive lubricant producers must also test sulfur content to meet regulatory limits, maintaining the performance and longevity of engine oils and transmission fluids. This testing is equally important for fuel exporters, where meeting the sulfur standards of different countries is critical for market entry.
Viscosity (ASTM D445)
Viscosity measurement is vital for refining, processing, and transportation efficiency. It impacts product performance, equipment wear, and regulatory compliance. With variations in market and fuel type regulations, viscosity-modifying additives must be tested alongside base fuels to meet performance standards without exceeding limits.
Pour Point (ASTM D97)
Pour point testing identifies the lowest temperature at which crude oil flows, vital for handling and transport in cold climates. It’s particularly relevant for producers and distributors of specialty fuels, like heating oil and kerosene. Pour point depressants, a common additive, are tested with base fuels to confirm cold-weather compliance.
The Role of LIMS in Crude Oil Testing
In today’s crude oil testing labs, LIMS (Laboratory Information Management Systems) play a central role in managing data and automating processes, helping labs handle the growing volume of tests and increasing regulatory demands. For QC and QA managers, LIMS simplifies sample data management - from tracking sample collection to organizing test results and analyzing key properties like distillation, sulfur content, and viscosity. By automating these processes, LIMS reduces manual data entry, accelerates batch tracking, and ensures quick access to comprehensive reports like Certificates of Analysis (CoAs), which are crucial for compliance.
For smaller labs, LIMS provides a streamlined approach to managing compliance and data integrity, boosting productivity while ensuring the accuracy and reliability of test results. It also simplifies compliance with standards like ISO 17025, enabling labs to meet evolving regulatory requirements efficiently while minimizing human error.
From managing sulfur levels in marine fuels to ensuring the right cetane number in diesel, LIMS supports efficient, consistent outcomes in every phase of crude oil testing.
Meeting QA, Compliance, and Competitiveness with LIMS
As environmental regulations tighten and industry standards rise, labs face mounting pressures to maintain product quality and comply with increasingly complex requirements, such as the IMO’s sulfur caps. LIMS helps address these challenges by improving data collection and centralizing workflows, supporting labs to meet regulatory requirements more efficiently. Whether managing sulfur levels or tracking other product specifications, LIMS helps ensure accurate and timely reporting, from Certificates of Analysis to regulatory documentation. For smaller labs, LIMS provides a competitive advantage by streamlining operations and enhancing compliance, while contributing to the industry's sustainability and regulatory goals.
Key Benefits of LIMS for QC and QA Managers:
- Increased Margins: Automating crude oil and product testing can improve yield accuracy and minimize the risk of off-spec batches. Workflow automation reduces the chances of a product recall or compliance violation, ensuring smooth operations across refining and production lines.
- Immediate Decision-Making: Real-time data monitoring enables rapid decisions regarding product quality across the board, from fuel terminals to packaged fuel manufacturers. This helps maintain consistency, reduces risk, and ensures that fuel quality at gas stations or distribution points meets market standards.
- Batch Testing: Batch testing in refining and petrochemical production means consistent quality, early issue detection, and improved safety. It’s a game-changer for fuel distributors and oil blenders, reducing waste and optimizing processes by providing batch-specific data.
- Global Coordination: For lubricant manufacturers, automatic comparison against specification limits allows global consistency, ensuring that engine oils and transmission fluids meet performance specifications quickly, no matter where they’re produced or sold.
- Reduced Operational Risks: With instant identification of quality deviations, LIMS helps prevent equipment damage, regulatory violations, and operational delays. Automated alerts support proactive corrective actions, reducing downtime and maintaining continuous production.
Conclusion
Robust crude oil analysis and quality control are essential for addressing the evolving challenges in the oil and gas industry. As environmental regulations tighten, supply chains fluctuate, and the push for sustainable fuels increases, labs must be efficient, responsive, and compliant. Automating workflows and data management with LIMS empowers QC and QA managers to address quality issues swiftly, reduce human error, and strengthen compliance efforts.
Automating workflows and processes with LIMS isn’t just about streamlining - it’s about enabling labs to respond swiftly to quality issues, reduce human error, and enhance compliance efforts. By harnessing automation and real-time data, labs can proactively manage quality, optimize performance, and gain the agility needed to adapt to shifting market conditions. Embracing these digital tools allows the industry to address regulatory pressures, improve operational efficiency, and capitalize on emerging opportunities in sustainable fuel production.
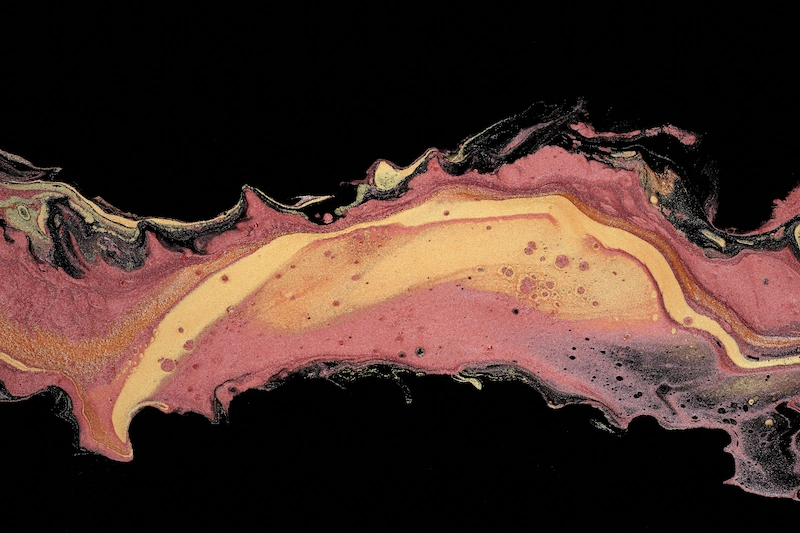